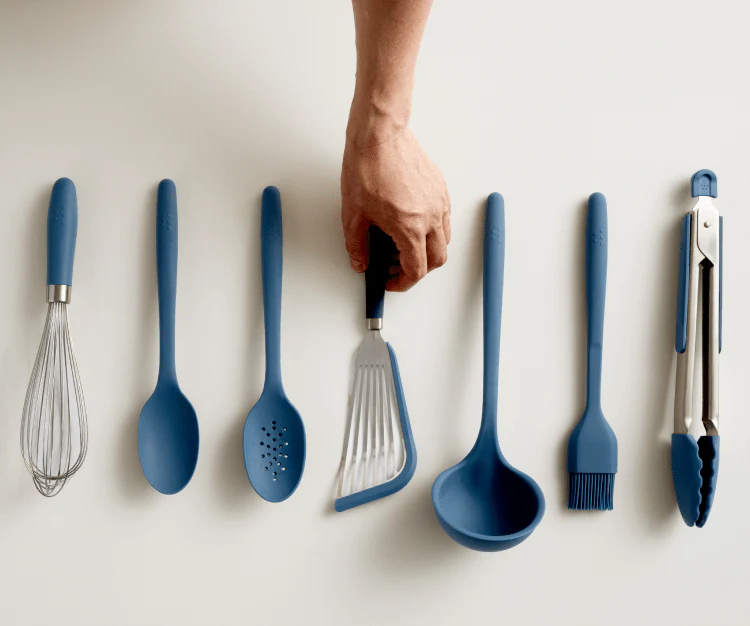
How Misen decreased product defects by 75% with FQ
Learn how Misen improved product quality across the board with Factored Quality's unified platform and QC services.
“Before Factored Quality, our quality process was reactive. Now, we have the structure to handle production issues, plus trusted inspection partners on-site who ensure our products are the best they can be.”
Founded in 2016, Nudient is a leading fashion tech brand for mobile accessories like phone cases, screen protectors, AirPods cases, laptop sleeves, and more. The Stockholm-based brand stands out with its sustainable materials and award-winning product design.
As Nudient expanded its product range and supplier network, it faced a hurdle: managing rapid growth with an increasingly complex operation. With revenue soaring and order quantities growing, they faced increasing pressure to avoid errors and maintain customer satisfaction. It was clear they needed meticulous quality checks.
Initial solutions to improve QC processes meant spending too much time communicating with consultants from other countries. Reporting customer complaints to suppliers was further complicated by a growing product catalog distributed worldwide across multiple warehouses.
To keep up, the Nudient team needed a QC solution that reflected the reputation they had built among customers without additional strain on their busy operation. That’s when they were referred to Factored Quality.
“Our processes had gotten too complex for the organization. We had four warehouses worldwide, and as more suppliers were involved, it was clear we couldn’t afford to have massive errors. The added complexity was driving costs and time.”
Unlike previous QC methods that relied on ad-hoc reactions to customer issues, Factored Quality introduced a structured and proactive system for on-site inspections. Instead of responding to issues as they happened, FQ helped Nudient implement documented quality checks that could be tied to each new product and high-volume order.
Working closely with FQ, Nudient crafted a company-specific checklist tailored to its product specifications and unique challenges. These checklists have reinforced their on-site inspections to ensure the best products with each batch across all customers, increasing confidence in their manufacturing process.
“By working with Factored Quality, we've standardized our quality checks and saved countless hours. It's tailored to our specific needs, so we know what to look for and will not be surprised by anything.”
By partnering with Factored Quality, the Nudient team not only boosted product quality, but they’ve saved significant time managing QC efforts. Plus, FQ’s user-friendly interface made communication simpler with fewer oversights. The results so far have been exceptional:
As Nudient continues to explore new product categories, the team sees its partnership with Factored Quality as a cornerstone for sustained growth and operational excellence as the brand expands to established and emerging markets.
“Factored Quality has been attentive to detail and solution-oriented since the beginning. Thanks to our partnership, we're saving time and money and feeling much more confident in our supply chain.”