compare factored quality
Why chose Factored Quality instead of relying on your supplier?
Factored Quality is the modern quality control platform preferred by brands – learn why we offer more support than just relying on your suppliers for QC.
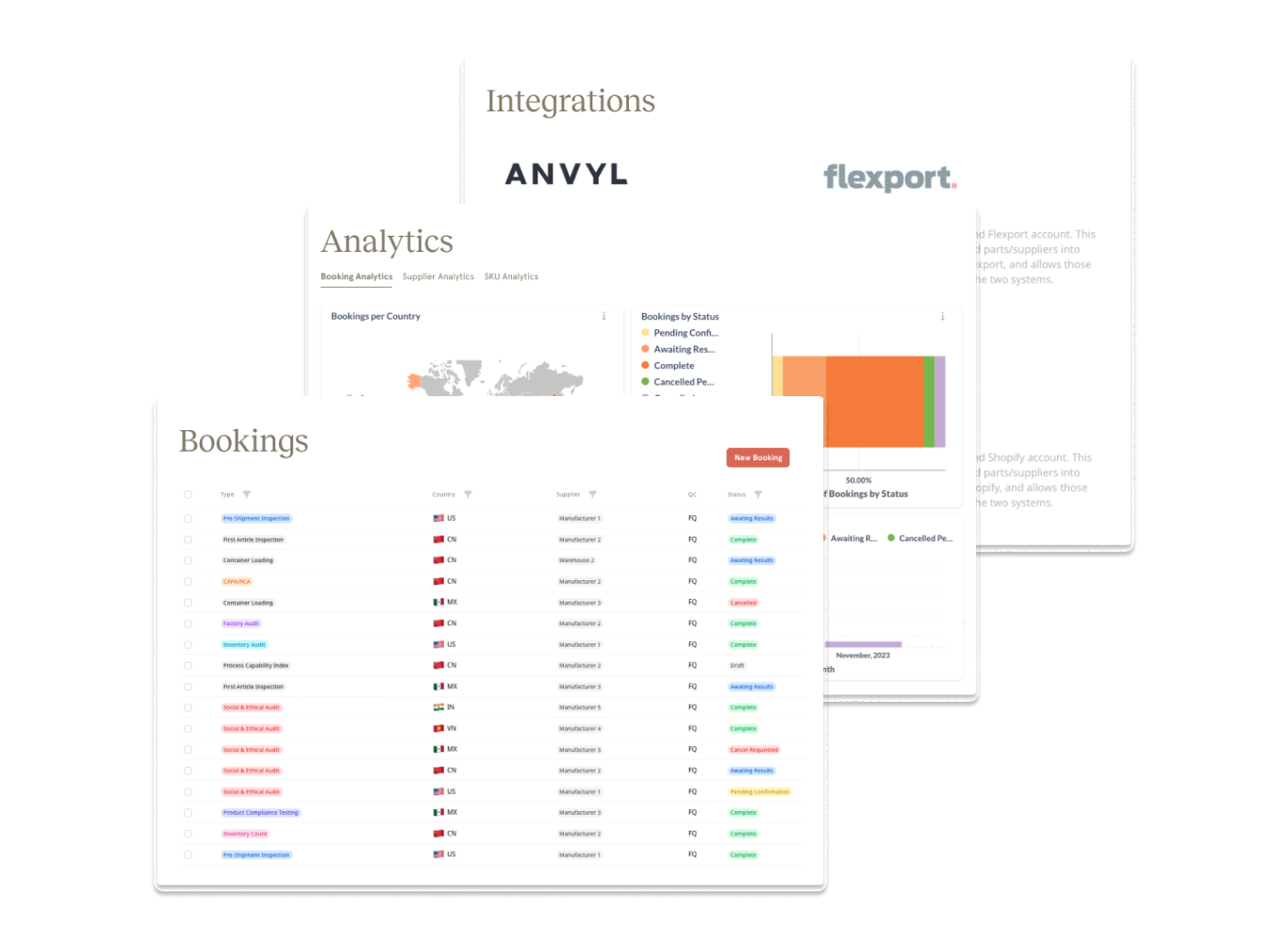
QUALITY CONTROL MADE SIMPLE
Here are the top four reasons why
Factored Quality offers more security than relying on your suppliers for QC:
VISIBILITY INTO THE QC PROCESS
Enhanced Transparency
When relying on suppliers for quality control, brands often suffer from a lack of visibility into the QC process. This can lead to unchecked errors, delayed reporting, and an overall lack of accountability. Factored Quality eliminates these issues by providing real-time updates and detailed reports through our advanced software platform. Without this level of visibility, brands are left in the dark, relying solely on supplier assurances without concrete evidence of quality standards being met.
DATA & ANALYTICS FOR QC RESULTS
Data-Driven Insights
Suppliers typically do not offer robust data or analytics to track quality control results, making it difficult for brands to identify trends, spot recurring issues, or make informed decisions. Factored Quality’s software delivers comprehensive analytics, giving you deep insights into product performance and factory efficiency. This data is crucial for continuous improvement and maintaining high-quality standards. Without such tools, brands must rely on anecdotal evidence and sporadic reports from suppliers, which can lead to suboptimal decision-making.
CONSISTENCY AND ORGANIZATION
Streamlined Processes
Supplier-led quality control often suffers from a lack of organization and consistency. Reporting can be infrequent, inconsistent, and sometimes non-existent, which hampers your ability to ensure products meet your standards. Factored Quality provides structured and consistent QC processes with regular, detailed reporting. Without this consistency, brands may face fragmented QC processes and storage of information in multiple areas, complicating the quality assurance process.
REDUCE DEPENDENCY ON MANUFACTURERS
Independent Assurance
Relying on suppliers for quality control creates a full dependency on the manufacturer, which can lead to conflicts and animosity if issues arise. This dependency also means that brands have little leverage in ensuring that quality standards are met consistently. Factored Quality offers an independent QC service, providing unbiased assessments and fostering a collaborative rather than adversarial relationship with suppliers. Without this independence, brands risk strained relationships and a lack of control over product quality.
factored quality vs RELYING ON YOUR SUPPLIERS
More reasons to choose Factored Quality
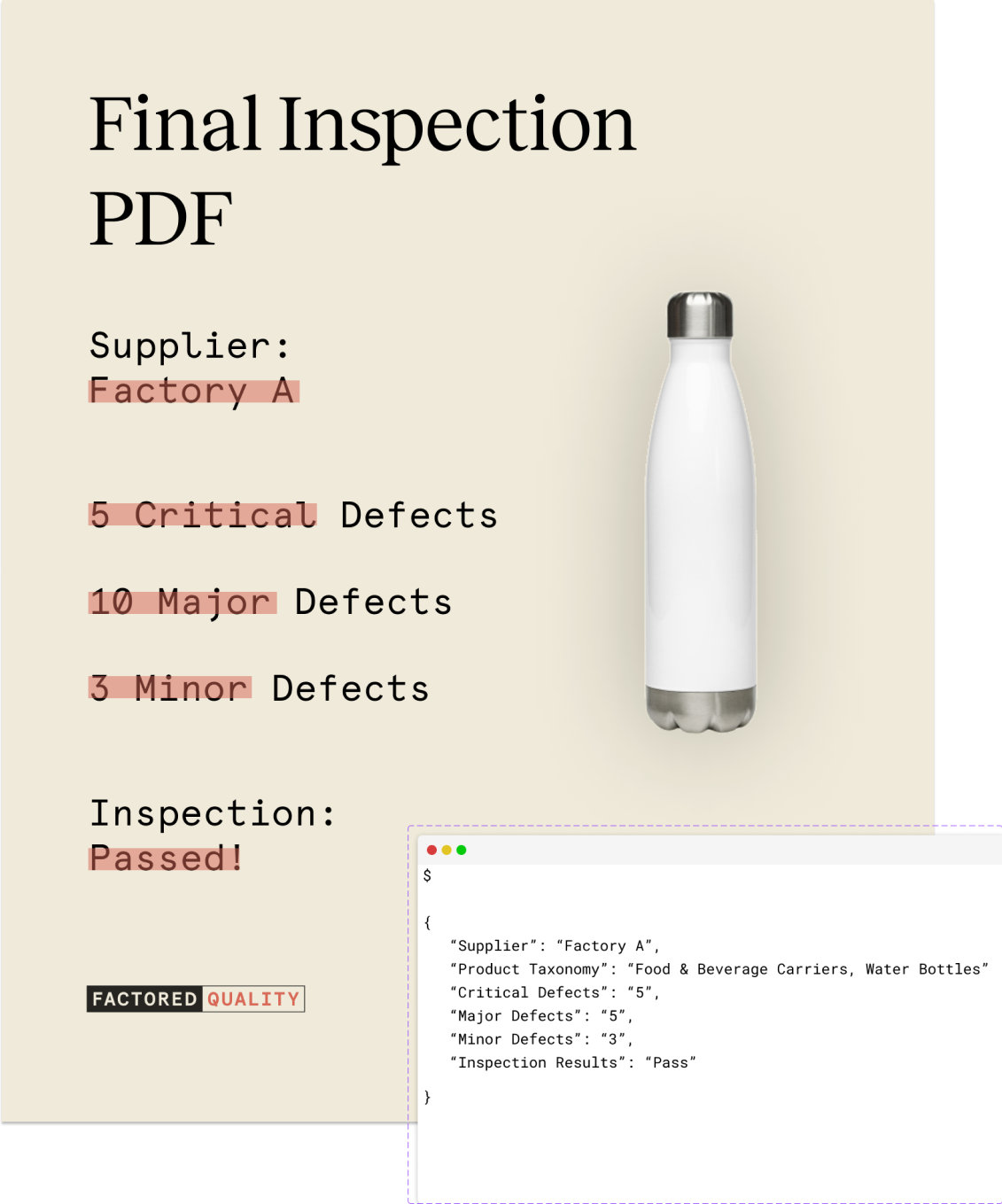
Document
Management
Management
Store existing reports or upload previously completed reports to the FQ platform. Sort reports by category, add dates, and set reminders for future QC inspections, supplier audits, and product testing.
.png)
Seamless
Integrations
Integrations
Automate the flow of your data in and out of the Factored Quality platform by easily integrating with your ERP, PO management systems, freight forwarders, and more.

Analytics + External API
Visualize and manage all of your product quality data in one interface with a filterable, customizable analytics dashboard. Or, extract this data from our platform and implement it within the tools of your choice.
“Leveraging Factored Quality is such a small cost in comparison to the potential downstream risks that it really is a no-brainer. De-risking your supply chain as much as possible is just the sensible thing to do.”
$70K+
saved in rework and shipping costs
17%
decreased returns by avoiding quality issues
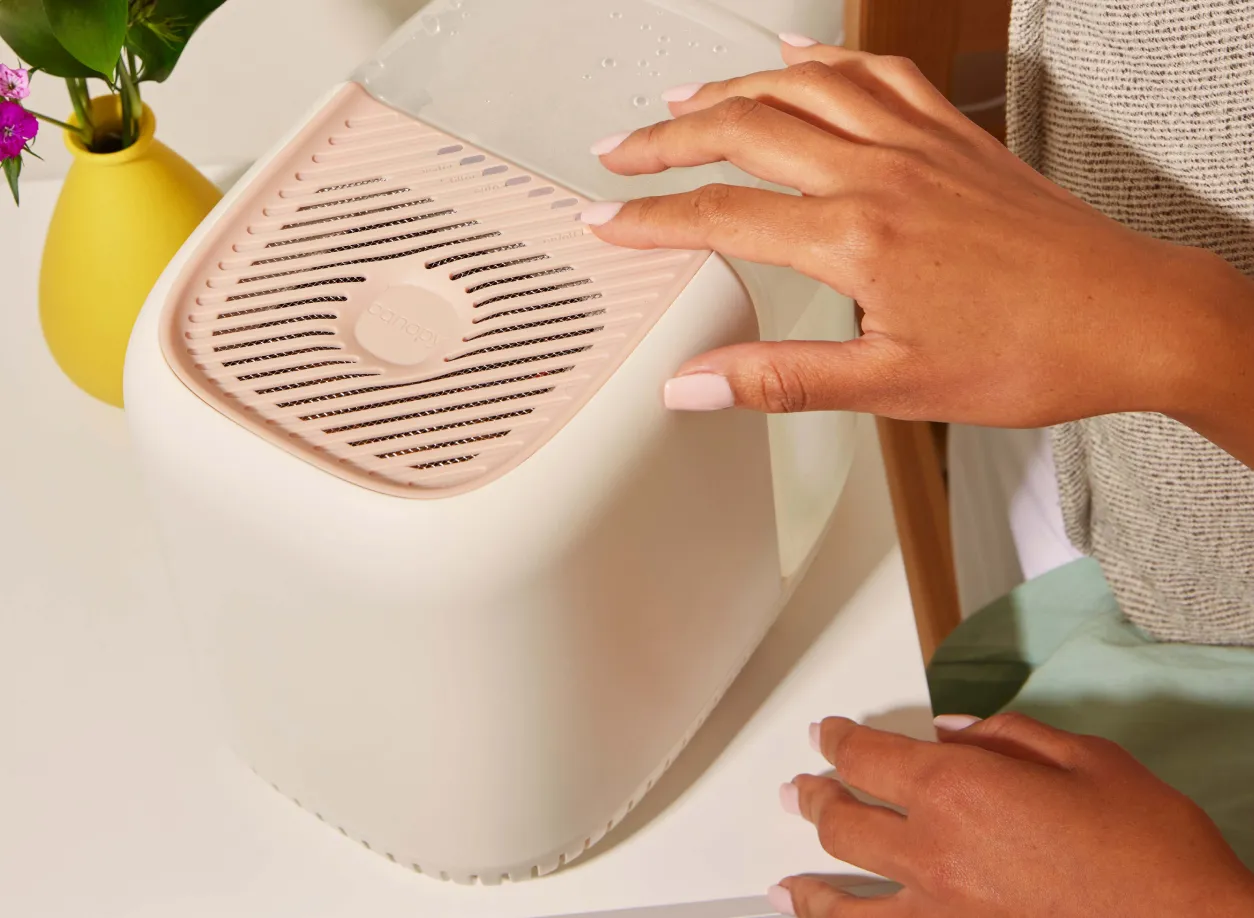
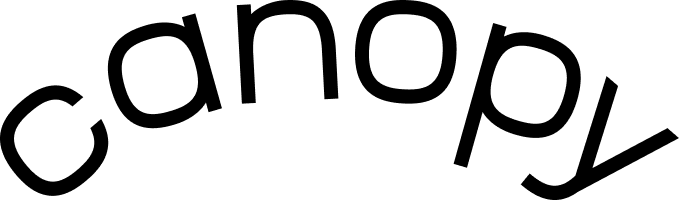