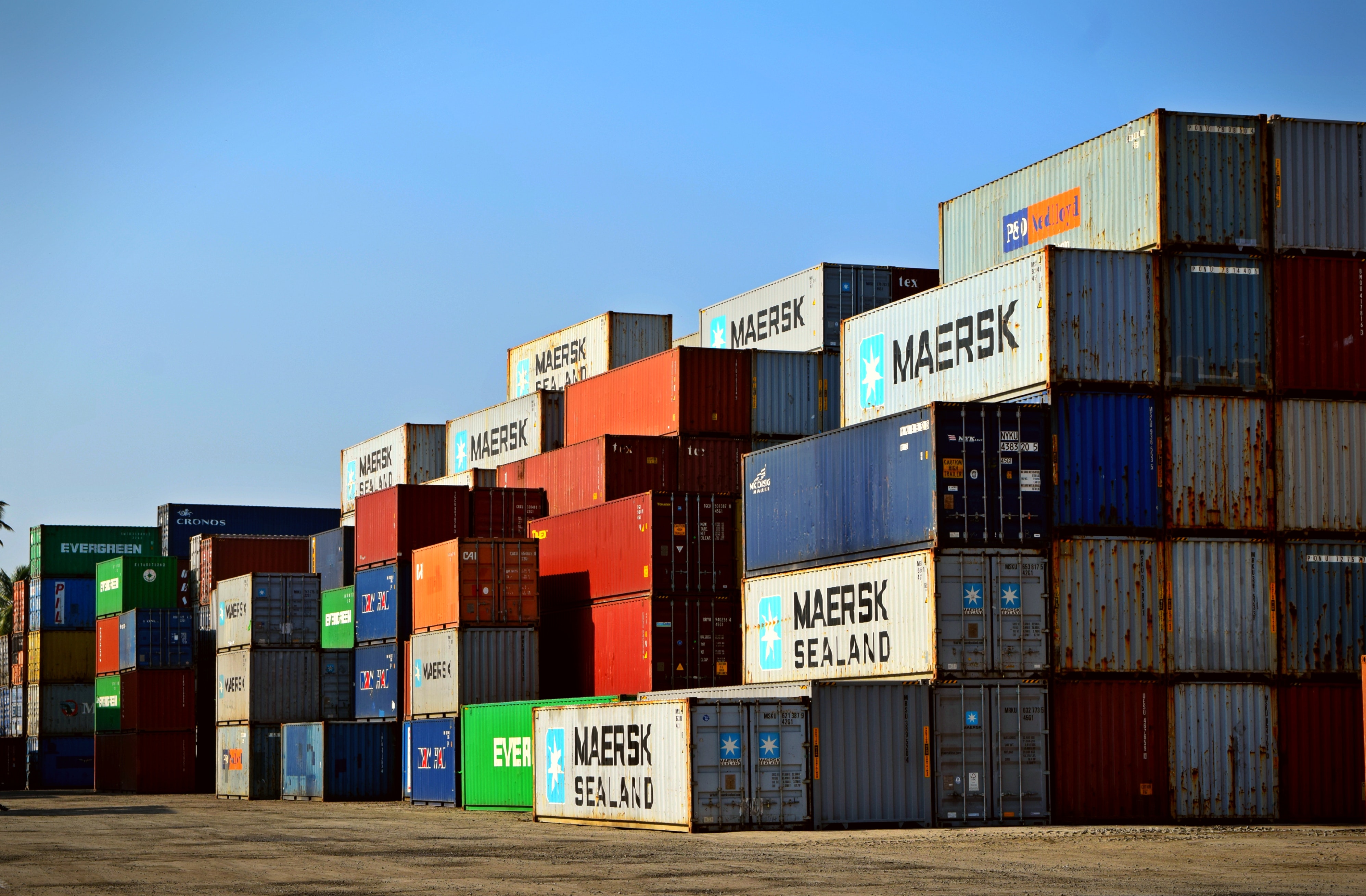
The Factored Quality Guide to MoCRA
In Part 7, we unpack the ins and outs of the Modernization of Cosmetics Regulation Act of 2022 and what it means for your brand.
How to ensure quality and consistency in your products with detailed inspections throughout the manufacturing process
For consumer goods brands, establishing a reputation for quality takes years of hard work and dedication. And if your products fail to meet strict standards due to negligence or poor internal workflows, the reputation you've established can vanish overnight. This is why quality control inspections are critical.
Rather than taking a reactionary approach — by recalling defective items or remaking entire batches — quality control inspections guarantee your products meet (or exceed) industry standards before they're shipped. While finding quality control inspectors and establishing internal workflows can seem like a daunting process, our team of QC experts is here to make it that much easier for your team.
A quality control inspection is a process that ensures your product meets both internal and industry standards. It follows prescribed steps to guarantee your product works as expected, is safe to use, and complies with relevant regulations.
Every inspection starts with a quality control checklist that tells the inspector exactly what to look for, from manufacturing tolerances to packaging requirements. This checklist also ensures inspections are consistent across batches and inspectors.
Once they've completed the tests, the inspector will document their findings in a quality report. These reports highlight potential quality control gaps, not only with individual products and batches, but also throughout your entire manufacturing process.
Inspectors are dedicated guardians of your brand's reputation, helping you exceed customer and industry expectations through meticulous attention to detail. They'll learn the intricacies of your product's specifications and production guidelines, helping identify quality control issues that would otherwise stay hidden while finding new ways to fix them.
Trusted quality control experts stay updated on key industry standards and regulations that may affect your products. They actively rely on this knowledge to ensure compliance both domestically and across foreign markets, helping brands expand their global reach without fear of fines or legal battles.
A close partnership with your inspector also lays the foundation for your brand to improve over time. Regular calls and meetings keep you informed of any inconsistencies in production, ensuring you can solve any quality issues before they become costly recalls.
Inspections do more than simply check a box; they help identify opportunities to improve your manufacturing processes, boost your reputation, and delight customers.
With a trusted quality control inspector and a well-defined inspection process, your brand benefits from:
Meeting regulatory requirements eliminates the risk of fines and ensures your products can enter new markets without additional legal hurdles. Plus, the penalties for non-compliance can be severe both fiscally and from a brand reputation standpoint. For example, a Chinese company recently launched an e-scooter in Europe that failed to pass a simple EU RoHS test — leading to the product being banned across all member states and severely impacting the brand’s reach and trustworthiness.
Detailed inspections don't simply judge the quality of your finished product and move on; they standardize every manufacturing step so you can expect uniform results across batches.
The process checks raw materials before they are used in production so your products maintain a high quality standard from the start. After products are built, safety inspections get hands-on to spot potential hazards before they can affect your customers. With properly inspected and packaged products, the risk of damage while in transit lowers—leading to fewer returns and greater customer satisfaction.
A commitment to regular inspections saves your brand from the hidden costs of manufacturing low-quality products. They protect your products from excessive defects, proactively solving any quality issues before you have to remake entire batches. Plus, regular quality control inspections reduce return rates, which have continued to plague consumer goods brands, as most returned products cannot be resold and are either destroyed or discarded.
Ensuring quality during the manufacturing process requires not one but many unique inspections. When used together, these five inspections cover everything from the start of manufacturing to shipping out the final batch.
In-line inspections are the standard method for reducing manufacturing defects during production. They audit the products being made and the tools and processes used to create them. For example, say you're a golf club manufacturer, and one of your milling machines is beginning to wear down. In-line inspections will catch this issue preemptively to ensure none of your products are shipped in a defective state.
Some examples of these quality control inspections include:
Pre-shipment inspections (PSI) occur when production is at least 80% complete. These evaluations check randomly selected samples from all batches to ensure they meet quality standards before shipping. They serve as a final opportunity to take corrective action before a production run is finished.
During a pre-shipment inspection, inspectors will:
Factory audits assess every detail of your supplier's facilities and processes, ensuring they comply with your quality standards, safety regulations, and ethical practices. They're best used to qualify potential partners and manage relationships with your existing supplier.
During these audits, inspectors cover the following steps:
Container loading checks ensure products are properly packed for shipment. Inspectors conduct a final review to prevent damage, loss, or contamination during transit — ensuring the cargo arrives at the destination ready for market.
These inspections typically require:
Compliance tests ensure your products meet all necessary domestic and international regulations. These tests are conducted by specialized testing labs that provide detailed reports to verify your product's compliance.
These inspections include:
If you're unsure which regulations apply to your products, tools like a compliance gap analysis can help you understand the scope of your unique needs.
Investing in trusted tools and experts makes it easier to guarantee your products' quality exceeds both industry and customer expectations. There are many useful resources on the market, but these four form a strong foundation to build upon:
Having the right software to manage your quality control inspections simplifies the entire process. With this tool, inspectors can schedule inspections, access your checklists and standards, and file their reports.
Quality control inspection software often integrates seamlessly with enterprise resource planning (ERP) and purchase order management tools. This integration unifies your data sources, allowing for real-time updates and comprehensive insights into product quality over time.
Finding a quality control inspector that your brand can trust is essential for guaranteeing quality over time. Look for inspectors who hold certifications from recognized bodies, such as ISO certifications or industry-specific qualifications.
Finding the right partner becomes easier with a little help. For example, Emulait sought a reliable quality inspector for their baby and children's products as they prepared to launch in Europe. Before they could release in the new market, every product needed to be certified compliant with the specific regulations of each member state.
Rather than try to find the right testing lab on their own, they partnered with Factored Quality. With Factored Quality's network of trusted compliance testing labs and safety inspectors, Emulait avoided testing errors during product certification that would have delayed their launch in EU markets.
Alexis Alban, Emulait's Director of Product and Brand, was ecstatic. “Not only was Factored Quality quick to respond and detail-oriented, but they had someone in constant communication with the lab,” he said. “And that person was available to answer all of our questions about product compliance.”
Comprehensive quality control checklists make your inspections simple. All your inspector has to do is follow predetermined steps, and they'll be able to guarantee quality consistently.
Start by explaining the specific attributes that define your product's quality, such as:
Quality control checklists must also inform the inspector of any relevant compliance needs and instructions for using appropriate testing equipment. Finally, make sure to add how your brand defines acceptable and unacceptable quality, including photos. You want it to be as easy to follow as possible when your inspector opens the list.
If you're creating a new checklist and unsure where to begin, tools like FQ's Digital Checklist Builder can simplify the process. With it, you can browse hundreds of preloaded checklists (complete with descriptions, pass criteria, and much more) or create your own custom options within minutes. You can also assign checklists to multiple SKUs in the booking flow, ensuring consistent inspections and greater control over quality processes.
Having expert partners throughout your supply chain ensures that quality control is integrated at every production stage.
Nobody can guarantee quality on their own. By partnering with exceptional inspectors and labs, you spread out the work without sacrificing that dedication to excellence. And finding ones you trust means you can focus on other areas of your business, like developing new products and enhancing your customers' experiences.
When selecting partners, look for those who offer personalized support and have a deep understanding of your industry's regulatory landscape. Prioritize companies with a proven track record and positive client testimonials. That way, your supply chain stays supported by professionals who are committed to your quality standards.
If you want to keep your focus on innovation, let Factored Quality cover quality control. Our software provides a central hub for everything related to quality control and product compliance. Plus, our network of expert QC partners is trained, certified, and vetted, serving as eyes and ears on the ground at your local manufacturing sites.
Get matched with one of over 2,000 pre-vetted experts and start building your inspection checklist today.